鄂钢130t转炉低铁耗低成本工艺实践
2024-06-17 11:25:27
目前,我国铁矿资源日益贫乏,进口矿石成本不断增加,大部分钢铁企业的铁水供应一直是生产的限制性环节。同时,国内机械、车辆、轨道、建筑等行业产生大量的废钢,且废钢的产量也在逐步增加。基于此,国内各钢铁企业对开发低铁耗、高废钢比的低成本转炉生产新工艺进行了诸多探索,最大限度地利用废钢资源,以解决铁水供应不足的问题。河北敬业钢铁有限公司通过调整钢铁料结构、优化炼钢工艺参数等措施,有效降低了生产成本;南京钢铁集团有限责任公司通过优化生产工艺流程和废钢种类,实现了转炉在低铁耗条件下稳定生产,同时减少了碳排放;宣化钢铁集团有限责任公司采取优化氧枪系统、扩大出钢口直径等手段,缩短了冶炼周期,实现低铁耗的快节奏生产;马鞍山钢铁股份有限公司通过物料平衡与热平衡计算,并结合现场试验研究,对操作工艺不断进行优化与改进,如调整铁水、生铁及废钢的装入量,实现转炉终点低成本精准控制;首钢集团及长治钢铁有限公司等采用炉内补热、降低出钢温度等方式,将铁耗降低至 845.04 kg/t,废钢比提高至20.65%;邯郸钢铁集团有限责任公司通过铁包加压块、改变炉料结构、转炉内预热废钢等措施,降低铁水消耗至 870 kg/t。综上所述,各钢厂通过调整钢铁料结构、优化工艺等操作,在降低了铁耗的同时,生产效率也得到明显提高。但有关低铁耗工艺对渣料消耗、终渣成分以及终点磷含量影响的研究鲜有报道。本文对宝武集团鄂城钢铁有限公司(简称鄂钢,下同)炼钢厂 130 t 转炉低铁耗生产进行研究,通过与常规铁耗生产模式各项指标进行对比,分析讨论了低铁耗工艺对渣料消耗、终渣成分以及终点磷含量的影响。
1 工艺装备
鄂钢炼钢厂现有 3 座转炉,主要生产条材及板材系列钢,其中,条材钢有螺纹钢、轴承钢、弹簧钢等,板材钢有低合金、容器钢、桥梁钢、海洋平台及船板钢等。产品广泛应用于水利、铁路及桥梁等行业。转炉生产所用铁水成分与温度如表 1 所列,不同钢坯废钢种类及含量如表 2 所列。转炉吹炼使用 5 孔氧枪,喉口直径为 42 mm,出口直径为 55 mm,马赫数为 2.02,喷头夹角设计为13°,供氧流量为 33 000~35 000 m3/h。转炉炼钢的金属原料包括铁水、废钢,辅料主要为石灰、镁球和白云石等。根据高炉铁水硅质量分数、温度等条件,选择合理的造渣工艺。
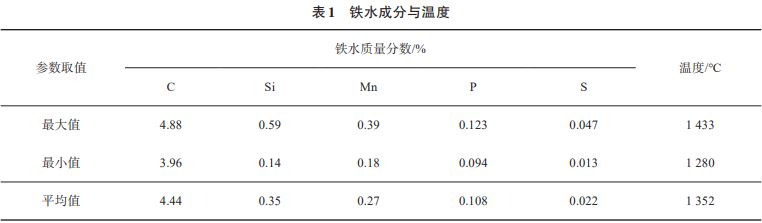
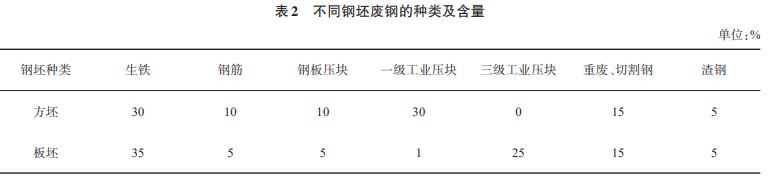
实施低铁耗低成本生产工艺首先要考虑冶炼过程中热量不足的问题。目前,鄂钢主要采用铁水罐加废钢、覆盖保温剂减少热量损失及外加增热剂等方法弥补冶炼过程中的热量损失。
2 低铁耗工艺试验结果
2.1 低铁耗工艺对出钢量及终点碳含量的影响
低铁耗工艺与常规工艺的装入制度及出钢情况如表3所列。与常规工艺相比,低铁耗工艺的铁水装入量降低了3.95t,废钢装入量增加了5.62t,出钢量增加了2.41t,出钢温度平均降低12℃,而转炉终点碳含量变化并不明显。

2.2 低铁耗工艺对辅料消耗的影响
低铁耗工艺与常规工艺的各项辅料消耗对比如表4所列。与常规工艺相比,低铁耗工艺的石灰消耗降低了2.44kg/t,镁球消耗降低了0.77kg/t,白云石消耗增加了0.26kg/t。
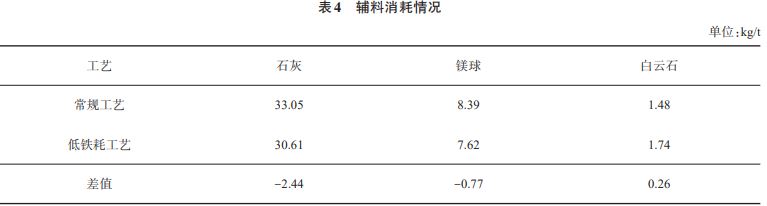
2.3 低铁耗工艺对转炉终渣的影响
低铁耗工艺与常规工艺的终渣成分对比如表5所列。低铁耗工艺条件下,终渣中的TFe(铁元素的含量)变化较显著,降低了1.76%;由于出钢温度的降低,有效抑制转炉后期回磷现象发生,终渣中P2O5含量增加;终渣中的MgO、MnO含量及碱度变化较小。
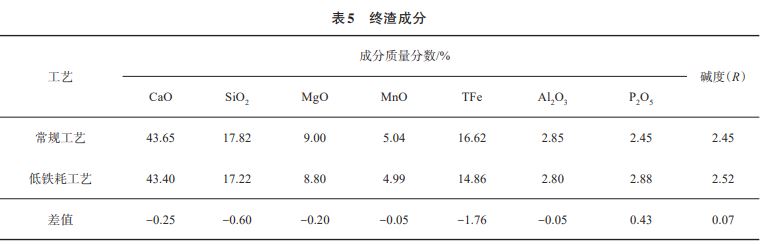
3 分析讨论
3.1 低铁耗工艺对出钢温度和终点碳含量的影响
铁耗对出钢温度的影响如图1所示。与常规工艺相比,低铁耗工艺转炉出钢温度主要集中在1600~1640℃之间,下降了约12℃。在满足出钢条件下,随着铁耗的增加,出钢温度逐渐升高。影响出钢温度的主要因素是铁水自身所带的热量以及铁水中硅、锰、碳等元素的氧化放热。由于低铁耗生产工艺中减少了铁水的加入量,从铁水带入的热量减少,从而导致出钢温度降低,同时,较低的出钢温度也能有效抑制回磷现象发生。
图2所示为铁耗对转炉终点碳含量的影响。两种工艺的终点碳含量都集中在0.05%~0.08%之间,说明铁耗的变化对转炉终点碳含量影响较小。因此,低铁耗工艺可以满足实际生产过程中钢种对终点碳含量的要求。
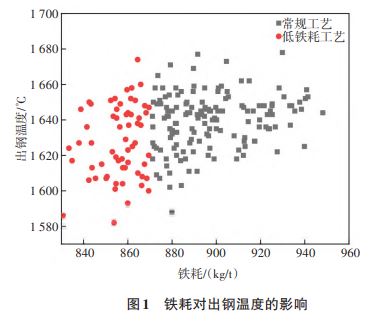
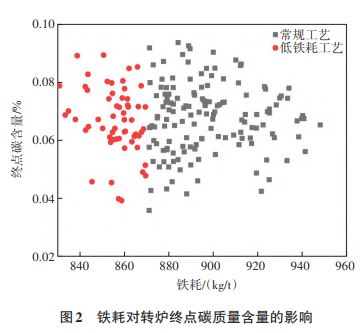
3.2 低铁耗工艺对辅料消耗影响
图3和图4所示分别为不同铁耗工艺下石灰和镁球的消耗量。与常规工艺相比,低铁耗工艺条件下石灰消耗量显著降低,为 2.44 kg/t,而镁球消耗量降低,为 0.77 kg/t。在转炉冶炼过程中,为完成脱磷任务,需要较高碱度(二元碱度R≥2.3)炉渣,因此,需要加入大量的石灰调节碱度。石灰添加量主要受铁水中硅元素质量分数的影响。在低铁耗工艺下,由于铁水量的降低,进入转炉的硅元素总量减少,这是导致同碱度的炉渣下,低铁耗工艺的石灰消耗量相应降低的主要原因。为避免对炉衬的侵蚀,炉渣中MgO含量需保持较高的水平,这也是导致低铁耗工艺相比于常规工艺在实际生产中镁球的消耗量相差不大的主要原因。此外,渣料消耗降低意味着总渣量的减少,可显著提高转炉的热利用效率,有助于提高废钢比,且总渣量降低,溢渣现象得到缓解,渣料利用率增加,同时还能提高 P 等杂质元素的去除率。
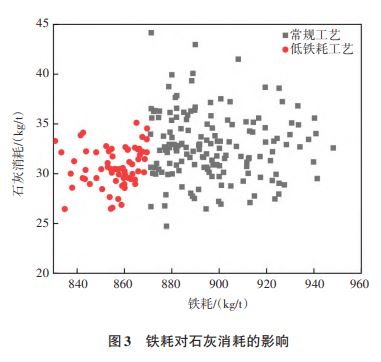
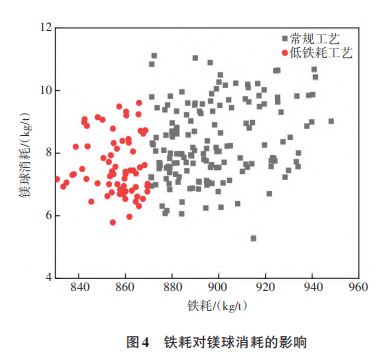
3.3 低铁耗工艺对转炉终渣的影响
图 5 和图 6 所示分别为不同工艺对转炉终渣TFe含量和碱度的影响。在实际生产过程中,两种工艺的终渣碱度无明显变化。与常规工艺相比,低铁耗工艺对转炉终点渣的成分变化主要体现在两个方面:①低铁耗工艺条件下,转炉终渣中 TFe 含量明显降低,平均降低幅度为 1.76%;②低铁耗工艺对终渣 TFe的控制较为稳定,终渣 TFe含量主要集中在 12%~17%,而常规工艺下的终渣 TFe 含量波动较大,部分炉次超过20%。终渣成分的控制显著影响钢液脱磷和钢铁料消耗,转炉终渣TFe含量是转炉冶炼控制水平的一项非常重要的技术指标。在转炉冶炼过程中,理论上应当提高吹炼初期炉渣全铁含量以迅速化渣,在吹炼末期降低全铁含量,达到降低终点氧含量和避免炉衬被侵蚀的目的。低铁耗工艺下终渣TFe含量明显降低,有利于降低钢铁料的消耗、烧损,提高金属收得率,并减轻炉渣对炉衬的侵蚀。
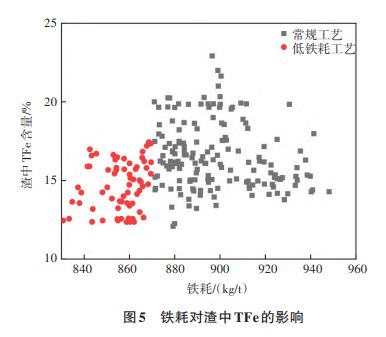

3.4 低铁耗工艺对脱磷率和终点磷的影响
脱磷是转炉冶炼过程中的主要任务之一。图7和图8所示分别为铁耗对转炉脱磷率和吹炼终点磷含量的影响。通过对比可知,低铁耗工艺的脱磷率较高,平均脱磷率达到77.9%,与常规工艺相比提高了8.1%。低铁耗工艺终点磷含量低于0.03%的炉次比例高达90%以上,远高于常规工艺炉次比例的50%。由此可见,脱磷率的提高和终点磷含量的降低验证了低铁耗工艺的脱磷效果更优。
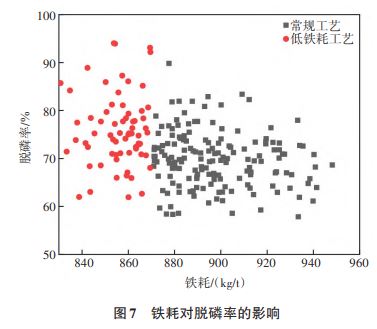
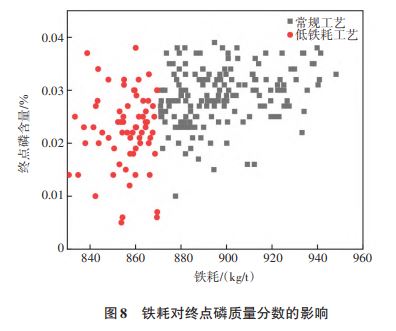
在转炉冶炼过程中,一般采用氧化脱磷的方式,主要是指通过氧枪吹入高纯度氧气,使钢水中磷与炉渣中氧化物形成稳定的磷酸盐,脱磷反应的方程式及平衡常数与温度的关系如式(1)、式(2)所列。
2[P]+5(FeO)+4(CaO)=(4CaO·P2O5)+5[Fe](1)
lgKP=40 067/T-15.06 (2)
式(2)中:Kp为平衡常数的数值;T 为温度的数值,单位K。
由此可知,较高 CaO 含量、较高 FeO 含量及低温条件均有利于脱磷,但炉渣中CaO含量过高易生成高熔点化合物 2CaO·SiO(2 熔点 2 130 ℃),FeO含量高又极易造成喷溅,且对转炉炉衬侵蚀严重。因此,转炉冶炼过程存在两个脱磷时机:一是在转炉冶炼前期,采用低温、低碱度条件进行前期脱磷;二是转炉冶炼后期,以较高碱度、强氧化性与大渣量促进后期脱磷。
在低铁耗工艺条件下,前期造渣过程中有效提高了渣料的利用率,增强了炉渣去磷效果;在冶炼后期,钢水温度低于常规工艺钢水温度,有效抑制了回磷现象发生。
4 结 论
本文通过介绍鄂钢130 t转炉的低铁耗工艺生产实践,通过对比低铁耗工艺与常规工艺对出钢温度、渣料消耗、终渣成分及终点磷含量等的影响,得到以下结论:
1)在低铁耗工艺条件下,转炉出钢温度主要集中在 1600~1640 ℃之间,平均出钢温度比常规工艺降低约12 ℃。
2)两种工艺的终点碳含量都集中在 0.05%~0.08%之间,说明铁耗的变化对转炉终点碳含量影响较小。
3)与常规工艺相比,低铁耗工艺的石灰消耗量降低了2.44kg/t,镁球消耗降低了0.77 kg/t,转炉终渣TFe含量降低了1.76%。
3)低铁耗工艺的平均脱磷率达到 77.9%,相对于常规工艺提高了8.1%;且终点磷含量在0.03%以下的炉次达到90%以上。
来源:江西冶金