宝钢湛江钢铁焦炉智能设备的应用
2024-04-18 09:57:53
1 焦炉背景概况
炼铁厂是宝钢湛江钢铁重要的组成单位,炼铁下设高炉、烧结、焦化、球团、原料5大单元,全流程的炼铁工艺。其中,炼焦单元一二期为:年产干全焦约340万t,采用4×65孔JNX2-70-2型复热式顶装焦炉,配套4×140t/h干熄焦设施、2×30MW抽汽凝汽式汽轮发电机组。三期为:年产干熄焦160万t,采用2×65孔JNX2-70-2型复热式顶装焦炉,配套3×140t/h干熄焦设施。其中一二焦炉配备推焦机、导焦机、装煤车、有(无)驱动运载车各3套,为2开1备使用;三焦炉新建推焦机、导焦机、装煤车和电车各2套,为1开1备使用。采用2-1串序对炭化室进行操作,其焦炉移动车辆按焦炉作业计划,首先由装煤车完成从煤塔下取出炼焦煤,装入炭化室,经过1个结焦周期,由推焦机启闭机侧焦炉炉门,同时由导焦机启闭焦侧焦炉炉门,并将成熟的焦炭推出炭化室导入旋转焦罐车,电机车驱动焦罐运载车到达牵引位,干熄焦牵引横移焦罐台车,送至提升机进行熄焦,熄焦直送高炉使用,蒸汽锅炉利用余热进行汽轮机发电。炼焦生产作业往往人机结合频率高,操作环境恶劣,作业风险高,容易出现机械伤人、灼伤、中毒等问题。
通过三焦炉智能设备及技术运用,操作人员可以按照手动、自动方式进行操作,结合焦炉本体的液压交换机,炉底巡检机器人,上升管余热利用及自动开闭和火落判定技术等功能相互配合,完成焦炉无人化生产作业。
2 三焦炉智能设备及技术应用措施
2.1 烟道废气脱硫脱硝净化装置
焦炉三期设置1套焦炉烟道废气脱硫脱硝净化装置,采用NaHCO3干法(SDS)脱硫+低温选择性催化剂还原法(SCR)脱硝工艺。该工艺先进行烟气脱硫,后除尘,然后低温SCR脱硝,实现焦炉烟道废气氮氧化物、二氧化硫、颗粒物、氨气等有害物排放符合超低排放要求,满足湛江钢铁A级标准。为减少系统阻力,按10万m3/h考虑煤气处理量。基本流程如图1所示。
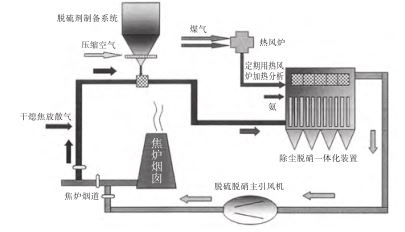
图 1 焦炉烟气脱硫脱硝装置流程
2.2 机车无组织排放达标
在设计时为便于现有车辆的通行及观察,没有对炉前挡风罩的后部挡板实行全密封设计,部分空气通过这些通道进入到炉前,会对炉头烟的收集产生一定影响。为实现车辆炉头烟收集全密封效果,满足超低排放无组织排放要求,对原有车辆进行全封闭改造,并增加机车除尘风机调节功能。
无烟装煤车可通过调节气动执行机构改变水封阀盘的开度,达到改变荒煤气流通截面积的目的,实现炭化室内压力的精确调节,保证各炭化室底部在全结焦周期内均处于微正压状态,避免炉门冒烟冒火及炭化室负压。配合车辆管理系统,完成上升管系统全自动装煤、推焦操作。
2.3 单孔炭化室压力控制系统
单孔炭化室压力控制系统在焦炉装煤生产操作阶段,集气管负压配合高压氨水喷射工艺,有效地控制烟尘的无组织排放。在焦炉结焦生产操作阶段依据荒煤气发生量曲线,把整个结焦过程分成11段调节给定值,更能精确控制炭化室底部压力在5~50Pa的范围内。在焦炉推焦生产操作阶段,炭化室与集气管完全阻断,避免推焦过程中吸入大量的空气,保证焦炉及后续工艺生产安全。系统与四大车系统数据交换,实现焦炉装煤、结焦、推焦过程的自动化。炭化室压力控制自动调节装置如图2所示。
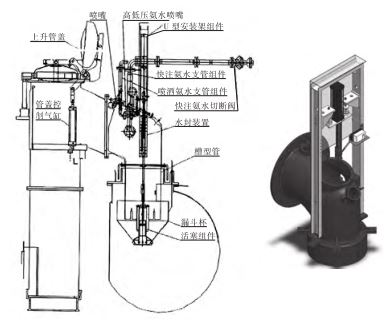
图 2 炭化室压力控制自动调节装置
2.4 焦炉炉底自动巡检小车
自动巡检小车携带工业视觉相机、热成像相机、CO传感器和温湿度传感器,可按预先设定的计划进行巡检,读取并自动记录巡检点的编码和准确日期,然后完成该巡检点预先设定的采集内容,再对采集的图像、环境参数等进行实时分析计算,将分析得到的设备运行状态、环境参数等结果通过wifi网络提交给部署在巡检专用服务器上的巡检管理系统软件。通过监控和采集炉底数据,完成焦炉区域无人化生产作业。图3为机器人巡检管理系统框架图。
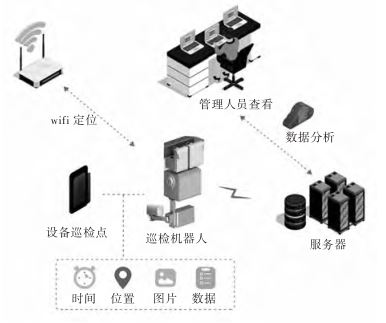
图3 机器人巡检管理系统框架图
2.5 机车自动化系统
2.5.1 机车相关应用技术
机车自动化系统主要包括以下几部分。
无人驾驶:粗定位编码器,通过自动对位系统进行走行距离检测和速度调节完成对位。精定位码牌,通过码牌编码,信号检测识别炉号并对中,定位精度±1mm。
智能防碰:采用毫米波雷达和激光-时间飞行原理及多重回波技术,非接触性检测,建立主动防碰撞系统。系统通过雷达扫描和激光回波,检测焦炉机车走行区域内人机实时信息,计算得出各车车距及车与障碍物或人的距离,并根据距离及趋势联锁车辆报警、减速、制动等车辆动作,避免车辆与周围目标物发生碰撞,保障车辆全自动作业时人机安全。
区域防控:焦炉整体区域进行分区规划,电子围栏,三级限制,分区管控。
振动扰度测量:在线对推焦杆振动、扰度测量,实时监控推焦杆使用情况。
结次焦检测:装煤车结次焦检测装置,为装煤车炉盖是否打开提供安全可靠的联锁保障。
小炉门检测:推焦机平面检测系统,提供小炉门开闭检测功能,保证平煤安全可靠。
液压碟刹:机车定位要求精准,刹车采用液压碟刹形式。
2.5.2 机车智能决策分析系统
机车智能决策分析系统包括系统管理、数据管理、推焦过程监控、生命周期管理、生产计划管理、专家诊断管理、能耗管理等。主要介绍以下几部分。
数字孪生系统:四大车数字孪生系统,采用数字化双胞胎技术,充分利用物理模型、传感器更新、运行历史等数据,在虚拟空间中完成映射,实现了焦炉机械设备实体向数字化模型的反馈,保证数字化系统与物理实物的协调一致。以三维的方式实时动态显示设备运行状态,实现了以“飞行”、“穿透”等“上帝视角”全方位查看设备的实时状态,并结合机车设备故障诊断系统,对机车设备长期监督、判断、分析等运行数据模型分析,提出合理化建议,提醒、辅助设备点检员对机车设备倾斜性管理。图4为数字化双胞胎技术的三维可视化。
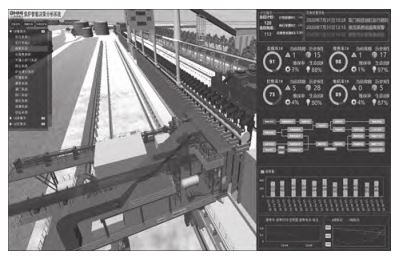
图4 数字化双胞胎技术的三维可视化
专家诊断管理:焦炉机车故障诊断,结合数字孪生和全流程监控及信息流控制,建立智能化的分析诊断系统,指导焦炉设备生产运行,使焦炉设备保持最佳运行状态,提高生产效率和经济效益。其中,智能诊断由大数据采集、远程数据连接、数据分析、专家诊断系统、分析报告输出等单元组成。其主要任务为关键数据采集,包括统计主要零部件的轴承、车轮转数,统计减速机使用时间,统计推焦杆、导焦栅、平煤杆使用次数,统计炉体温度、压力、荒煤气发生量,及机车推焦电流或推焦力,最终形成数据库,便于焦炉生产、配煤等系统的优化。
能源管理:包括对水、电、气、液压介质、润滑介质消耗量进行数据采集与分析。在线监测能源介质压力、流量、清洁度,对能源介质消耗监控,保证能源量最小;对介质清洁度进行监控,形成数据库。
生命周期管理:备件周期管理,以宝钢设备管理为基础,预知状态维修为指导,结合设备使用说明书的推荐,对设备寿命进行专家系统评测,智能指导维修、保养。对设备进行故障预诊断,形成数据库,便于设备维护保养。
2.6 通讯技术
无线数据系统由控制信号无线数传和视频5G无线数传2个部分组成。控制信号无线数传用于车上PLC控制系统与地面协调系统间的数据通信,视频无线数传用于车上摄像头信号与车上PLC控制系统的传输。无线数传系统由地面基站及天线、车载站及天线、数传机柜及网络等设备组成。地面基站及天线的布置应完全覆盖车辆工作区域,无信号盲区,通信宽带满足数据信号和视频信号的实时可靠传输需求。
炉顶自动控制、地下巡检机器人、四车综合联锁,监控系统数据传输利用5G数据完成。
2.7 炉顶辅助功能
炉顶辅助功能包括炉顶测温、火落判定、加煤口堵塞检测、上升管余热回收利用、炭化室单孔调压系统等。在加煤口安装探头装置,用温度判定方法进行检测,在取盖机构侧旁安装红外激光检测器,探测每个加煤口,通过温度判别加煤口盖是否正常开启,加煤口是否存在堵塞现象。
3 焦炉无人化前景
随着设备水平不断的提高和自动化技术的迅速发展,炼焦生产工艺自动化研究也越来越深入,虽然实现机车无人驾驶越来越多,但短时自动、监控密集、区域封闭并不是真正的无人驾驶,设备的智能分析、节能环保、状态保持等因素,直接影响到焦炉机车无人驾驶的实现。
(1)天气对焦炉设备的制约性。地域特性不同,限制因素多种多样,黑天、白天、雨天、大雾、大风、雪、台风等天气状况,对焦炉机车生产运行有着很强的制约性。如雨天模式车辆刹车性能下降,大雾天摄像头视线受阻,黑天部分区域需自动照明等。焦炉智能化应结合气象预报,提前做出预判作业或不同环境作业模型。
(2)智能辅助设备的应用。焦炉生产目前仍需炉体维护、巡检点检等人员,利用智能化机器人、红外热成像等技术,代替现有辅助人员巡检作业,也是无人化需要解决的重要问题之一。
(3)数字的智能化。现代化全流程智能信息流控制设备已进入数字化时代,通过数据的分析和判断,即可做出正确的选择,但数字信息的自我校正和纠正如何做到100%,也是无人化的重要一环。
(4)无人化并非代表无人,但是如何把点检员变成维护工程师,把生产人员变成流程工程师,高尖端人员的培养和能力,更是不可缺少的关键,人机结合才是完美实现焦化无人生产的最终结果。
4 结论
炼铁厂焦炉通过无人驾驶、智能防碰撞、区域防控、安全联锁、无线技术、集群操作模式、结次焦检查等多种技术的应用,并结合焦炉本体的防爆液压交换机、炉底巡检机器人、上升管余热回收、上升管自动开闭和火落判定技术等功能相互配合,全流程监控智能分析操作及控制,实现焦炉机车的自动化、少人化,同时提高生产作业效率,确保区域生产安全,最终实现焦炉区无人化生产。