宝钢湛江钢铁炼铁厂环保新工艺技术应用
2015-11-05 09:34:32
随着一系列环保新规划、国家标准的出台和广东地区对环保新的要求,湛江钢铁大气污染物排放于2014年起执行新的特别排放标准。针对环保要求的变化,湛江钢铁不断优化环保设施设计,在铁前工序采用了多种环保新工艺技术,以满足国家排放标准(见图1)。
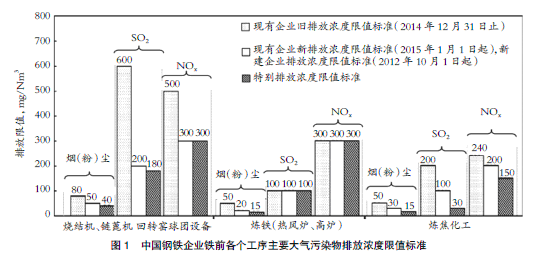
1 原料场防尘新工艺技术
原料场主要承担了各个工序所需散状原燃料的装卸、贮存、加工和输送任务,粉尘是其主要的污染物。
针对装卸和贮存可能产生的粉尘污染,湛江钢铁的混匀料场、1个原料贮存料场和3个煤贮存料场均采取了封闭措施;1个贮存铁矿粉的条形露天堆场,增设了20m高的防风网,利用空气动力学原理,使风速在防风网内衰减,减小起尘率,有效阻挡粉尘迁移。原燃料的破碎加工配套了高效的布袋除尘设备。原燃料输送采用封闭式皮带机通廊输送(约2.6km)和转运站微雾抑尘装置来控制粉尘污染。微雾抑尘原理是利用直径为1-10μm的水雾对悬浮在空气中的粉尘尤其是PM2.5等可入肺粉尘进行有效地吸附团聚,并在重力作用下沉降。
此新工艺减少了粉尘的收集和输送,直接在源头抑制粉尘的扩散。通过以上工艺的应用,原料场的粉尘排放值可达到≤15mg/Nm3。
2 炼焦烟气净化技术
湛江钢铁配置了4×65孔7m的顶装焦炉,单座焦炉烟道废气(180℃)量约为0.26×106Nm3/h,其中:烟(粉)尘浓度约为20mg/Nm3;采用混合煤气作为燃料燃烧后的SO2含量约为80mg/Nm3;采用废气循环和分段加热的燃烧控制技术后NOx可降至约500mg/Nm3。然而,烟气中主要的废气污染物仍无法满足国家特排标准的要求,必须对焦炉烟气进行脱硫脱硝净化处理。目前,国内外针对焦炉烟气的脱硫脱硝技术尚处于研发阶段,还未有工程应用实例。热电厂烟气的脱硫脱硝技术应用较为成熟,主要为“NH3-SCR烟气脱硝+石灰石湿法脱硫”工艺,若炼焦采用相同工艺,焦炉烟气温度相对较低,采用中温脱硝(300-400℃)的钒系催化剂的脱硝效率会很低,需大幅加热烟气;烟气中的SO2在200-250℃极易生成具有腐蚀性的硫酸氢铵,致使催化剂中毒;采用湿法脱硫后的烟气温度会低于130℃,不能直接从烟囱上升排放。根据这些不同之处,湛江钢铁炼焦工序采用了“旋转喷雾半干法脱硫+低温选择性催化还原法(NH3-SCR)脱硝除尘”工艺,成为世界上首个对钢铁企业焦炉烟道废气脱硫脱硝的工程应用实例。
炼焦烟气脱硫脱硝的工艺系统主要由脱硫塔、除尘脱硝一体化装置、喷氨系统、引风机、热风炉和烟气管道等组成。两座焦炉排出的烟气(约180℃)首先进入旋转喷雾脱硫塔,雾化的Na2CO3饱和溶液与烟气接触迅速完成SO2的吸收,脱硫效率在80%以上;脱硫后烟气进入一体化装置时先经布袋除尘,再由一体化装置配备的烟气加热模块加热至200℃后,与喷入的NH3还原剂充分混合;混合后的烟气进入低温脱硝催化剂模块层,在催化剂作用下NOX被NH3还原为无害的N2和H2O,脱硝效率不低于80%;净化后的洁净烟气(>160℃)经过引风机送烟囱排放,小部分烟气通过热风炉小幅加热后回用到一体化装置烟气加热模块中。该工艺采取先脱硫的模式可以有效控制后续脱硝硫酸氢铵的生成,为低温高效脱硝创造条件;一体化装置可以集中进行除尘、加热和脱硝,减少管道输送的热损耗,模块化可提高脱硝操作和检修的灵活性;采用低温脱硝催化剂可使脱硫后的烟气仅需小幅加热即可进行高效率地脱硝。此外,160℃以上的排气温度不会在烟囱周围产生烟囱雨,并可以避免烟气温度低于酸露点而引起的烟囱腐蚀。
3 烧结烟气净化技术
烧结工序新建的两台烧结机均为550m2,单台烧结机烟气量达1.8×106Nm3/h,烟(粉)尘浓度约120mg/Nm3,SO2为300-1000mg/Nm3,NOx为100-500mg/Nm3,较之焦炉烟气量大得多,产生的大气污染物浓度也高。烧结烟气量、温度和含水量波动较大,还含有二恶英、SO3、HCl、HF和重金属等污染物。
传统的湿法石灰-石膏工艺仅能满足脱SO2的需要,产生的废水中重金属等污染成分难以处置,对NOx的处理若选择增加NH3-SCR脱硝工艺,则加热烟气能耗太高。因此,根据烧结烟气的特点,湛江钢铁烧结工序选择了活性炭吸附脱硫脱硝工艺净化烧结烟气。该工艺的原理主要是利用活性炭比表面积大、具有大量微细孔的特点,首先对粉尘、SO2、NOx、二恶英和重金属等有害物质进行物理吸附;再利用微细孔内活性炭表面存在的一定量活性键位催化NOx和NH3的反应生成N2和H2O;吸附于活性炭的SO2和重金属等通过再加热脱附,二恶英苯环间的氧基在活性炭表面催化下被破坏裂解为无害物质,活性炭实现再生。
烧结烟气净化系统主要由烧结机头电除尘、引风机、吸附塔、解析塔、喷氨系统、活性炭输送系统、制酸系统和烟气管道等组成。烧结机产生的烟气首先经过电除尘器脱除大部分烟(粉)尘和重金属物质,再由增压风机将烟气引入若干个相对独立的吸附塔中。在吸附塔内,烟气与稀释的氨气混合通过由活性炭颗粒填充的网格层,大部分粉尘、SO2、二恶英和重金属被活性炭吸附,NOx与NH3反应转化成N2和H2O后的烟气经烟囱达标排入大气中,活性炭由输送机送至解析塔。解析塔上部通过隔层加热将活性炭加热至约400℃,SO2脱附后富集送至制酸系统,二恶英降解;下部冷却筛分后的再生活性炭可返回吸附塔内继续循环使用。系统可通过调节吸附塔内活性炭填充量和下料速度灵活地应对烟气的变化,有效地回收利用SO2,保证脱硫脱硝的效率。
4 球团烟气净化技术
链篦机-回转窑球团工序烟气排放量可达1.4×106Nm3/h,烟(粉)尘浓度约为100mg/Nm3,SO2为100-1000mg/Nm3,NOx为150-200mg/Nm3。烟气中SO2和NOx主要产生于回转窑煤燃料的供热燃烧,NOx的排放浓度约100-150 mg/Nm3(小于国标特排限值),目前阶段暂不需要考虑脱硝处理。湛江钢铁球团烟气中SO2的脱除采用了LJS循环流化床法,该工艺已在宝钢股份和梅钢的烧结机脱硫得到成熟应用。工艺原理主要是絮状的脱硫剂在激烈湍动中不断解体重新被气流提升,物料在循环流化床内气固两相激烈地湍动与混合,气固间的滑落速度高达单颗粒滑落速度的数十倍,极大地强化了传质与传热,加之床内高达50以上的Ca/S比,SO2可与Ca(OH)2 充分接触反应并生成CaSO3·1/2H2O和H2O,烟气中微量的SO3、HF、HCl和重金属等污染物也在流化床内被反应或吸收。
LJS循环流化床脱硫工艺系统主要由电除尘器、脱硫剂添加和雾化装置、循环流化床反应器、布袋除尘器和烟气管道等组成。烟气首先通过电除尘器脱除大部分烟(粉)尘和重金属物质,再通过增压风机与脱硫剂一起输送至循环流化床反应器。流化床底部烟气入口设有雾化喷水装置,可将烟气温度降至SO2与Ca(OH)2反应的最佳温度(80℃)。脱硫剂和循环脱硫灰在塔内进行充分反应。无论烟气量如何变化,烟气在流化床下部文丘里以上的塔内流速均保持在4-6m/s,烟气停留时间在6s左右,可保证高的脱硫效率(≥90%)。脱硫后烟气经布袋除尘,气固分离的脱硫灰可返回流化床内继续参加反应,净化后的烟气通过烟囱达标排放。流化床中气固之间良好的传热、传质效果使得绝大部分硫化物得以去除。用于降低烟气温度的雾化水附着在巨大比表面积的脱硫剂颗粒上进入流化床,在塔内得到充分的蒸发,保证进入后续除尘器中的灰具有良好的流动状态。此外,烟气中的脱硫剂在滤袋表面沉降形成滤饼,延长了脱硫剂与酸性气体、有机污染物等的接触时间,增加了对酸性气体、重金属和二恶英等有害物质的脱除率。
5 高炉环保新工艺技术
湛江钢铁5050m3高炉荒煤气排放量为1.25×106Nm3/h,粉尘浓度高达10-15g/Nm3,
对荒煤气的回收净化主要采用了重力除尘和干法除尘工艺:炉顶荒煤气首先通过上升管和下降管输送至重力除尘器,利用气流流速和方向的突变,借助重力和惯性力沉降脱除较大粒度的颗粒物,将粉尘浓度降至约10g/Nm3;再经多模块并联的外滤式布袋干法除尘器净化,粉尘浓度可降至5mg/Nm3。干法煤气净化与湿法相比:无废水产生;煤气压降小,余压发电量可提高30%以上;含水量低、温度高,作为二次能源具有更高的热值。热风炉采用高效陶瓷燃烧器和减小格子砖孔径、控制合理燃烧温度和温度场均匀分布等新技术,减少了NOx的产生量,净化后的高炉煤气作为热风炉燃料在燃烧过程中产生的烟气粉尘为5mg/Nm3,SO2和NOx分别为120mg/Nm3和50mg/Nm3,可通过烟囱达标排放。
针对初始浓度达3g/Nm3的高炉出铁场出铁时产生的烟气,湛江钢铁设置了两套1.2×106Nm3/h的烟气除尘系统,经袋式除尘净化后的烟气粉尘浓度(≤20mg/Nm3)可达到排放标准的要求。对于开堵铁口烟尘、一次除尘未捕集到的烟尘及高炉炉顶上料主皮带机头部、炉顶受料斗处工作时产生的粉尘,在炉顶除尘系统的基础上新增了炉顶罩,设置于车间的屋脊处,利用顶棚下受限气流自发向高处运动并积聚的特性将烟气引流至炉顶除尘系统,提高了炉顶除尘系统的烟气捕集效率。
同时在炉顶采用TGR炉顶煤气循环技术,对料罐均压后泄压排放到大气中的煤气进行回收,有效减少了煤气和粉尘的排放。
6 结语
新建的宝钢湛江钢铁有限公司严格依据国家和地方的环保要求,落实最环保的“绿色碳钢板材生产基地”的社会承诺,对大气污染物排放占比较大的炼铁厂各个工序生产采取了较为全面的防治措施,针对不同工序各自的特点合理地选择环保工艺技术,实现了排放达标。