重钢中厚板表面微裂纹成因和预防措施分析
2014-09-12 08:50:19
通过系统分析连铸板坯轧成中厚板表面微裂纹的形成原因,查找对裂纹形成具有明显影响的主要因素。重钢通过采取优化结晶器保护渣结晶性能设计,做好传热的控制;强化结晶器铜板倒锥度和保持宽面铜板夹紧,减少初生坯壳的凝固后受力不均匀性;加强结晶器足辊和弯曲段的对弧精度控制,防止板坯角部过度受力;强化生产调度,确保供钢节奏;改进开浇及换水口操作,缩短板坯在低拉速下的运行时间,减少坯壳过冷;注意钢中碳、铝等成份控制,降低钢的裂纹敏感性等措施后,中厚板表面裂纹得到较好控制。
连铸板坯轧制成中厚板有一些常见质量缺陷,表面微裂纹是钢质缺陷的最主要类型,其一旦出现,将导致该块钢板成为非计划品甚至废品,对应的供货合同也无法及时兑现,打乱了生产秩序,严重影响企业的声誉和市场竞争力。重钢一炼钢厂2013年供4100轧机的板坯量为1636358.079t,约占全厂产量的30%,其产品主要为中碳亚包晶钢,在高拉速下生产具有较强的裂纹敏感性,微裂纹非计划品达0.82%。本文就裂纹缺陷的成因及影响因素进行分析,以提出针对性强的预防措施,进一步降低钢板表面微裂纹发生率。
1、钢板表面微裂纹的基本情况
1.1、裂纹非计划品按厚度和时间分布
钢板表面微裂纹非计划品按厚度分布情况是:40-60mm厚度的钢板小纵裂纹率5.317%;>60mm厚度的钢板小纵裂纹率3.388%;>60mm厚度的钢板横裂纹率1.996%,为主要缺陷;其余均低于1%。
钢板表面微裂纹非计划品按板坯生产时间分布情况如图1所示。2月和7月尤其突出,9月后逐渐下降,10-12月各类裂纹得到明显控制。

图1:按板坯生产时间分布的钢板表面微裂纹非计划品率
1.2、裂纹非计划品按钢种和板坯断面分布
各钢种微裂纹非计划品分布情况如图2所示。Q390GJC小纵裂纹超过1200t,A钢超过1100t,Q345B超过700t,16MnDR超过600t,A36、E40超过400t;边部横裂纹D36超过900t,A32超过700t,A、E40超过400t;钢板表面横裂纹E47超过600t。各断面板坯所轧钢板表面微裂纹非计划品中,3号机生产板坯占94.90%,其余为1、2号机生产。
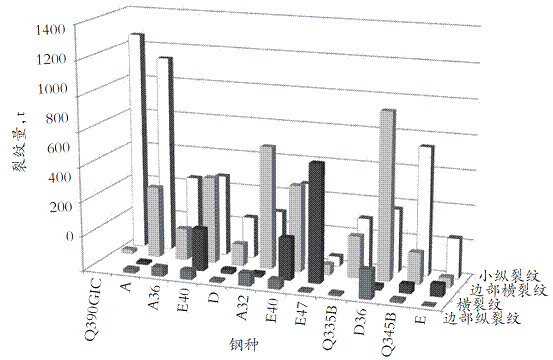
图2:各类钢种微裂纹非计划品分布
各断面板坯所轧钢板表面微裂纹分布情况如图3所示。250mm×2010mm等断面小纵裂纹率较高,300mm×2000mm等断面角部横裂纹率较高,300mm×2010mm断面横裂纹率较高,250mm×2010mm等大倒角断面板坯角部横裂纹率相对较低。
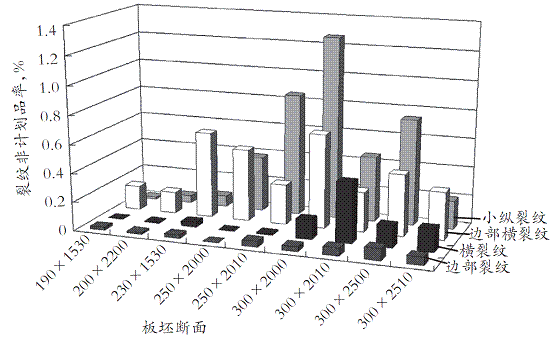
图3:各断面板坯所轧钢板表面微裂纹分布情况
2、厚钢板小纵裂纹分析
取有表面疑似纵裂纹的厚钢板试样进行缺陷金相分析,发现缺陷处有氧化质点和严重氧化铁,未发现有夹杂,厚度方向深度较浅,在0.1-0.3mm之间,判定该缺陷为裂纹。
对应的炉次取板坯进行表面酸洗和刨削,发现板坯表面有小纵裂纹存在,经过刨削后确认厚度约2-3mm之间,酸洗后板坯表面如图4所示。试样刨削后状况如图5所示。
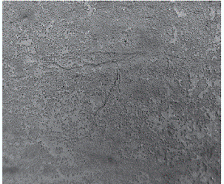
图4:对应炉号酸洗后的板坯表面纵裂纹
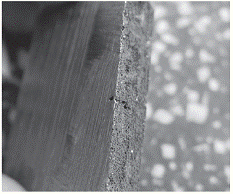
图5:酸洗后的板坯表面纵裂纹刨削状况
3、微裂纹成因
3.1、小纵裂纹
钢水流入结晶器后,因凝固时收缩率高,弯月面下100mm内冷却不均匀,形成的初生坯壳厚度极不一致,厚度较薄区域的凝固界面处应力集中而产生裂纹,在二冷区内纵裂纹并未迅速扩大,板坯精整时深度不超过5mm的微裂纹因氧化铁皮覆盖不容易发现而未能清理,在轧制时遗留于钢板表面导致裂纹出现。
3.2、边部纵裂纹
钢水在结晶器内凝固过程中,宽面铜板对坯壳的夹持或窄面铜板对坯壳的支撑不良,在偏离角部附近坯壳较薄处凝固界面产生内部纵向裂纹,位于板坯表面的皮下,轧制时金属流变后裂纹暴露出来,成为边部纵裂纹。
3.3、角部横裂纹
板坯经过结晶器足辊和弯曲段接弧区域、弯曲段弯曲区域、矫直段的矫直区域,角部表面温度正好处于700-900℃的第三脆性区,铝、铌等元素的碳氮化物在晶界析出导致钢的延性下降,角部横裂纹产生。
3.4、横裂纹
含铜、铝、铌钢因拉速低,遇碳等元素综合作用,收缩率较高,因拉速低或二冷区冷却强度偏大,板坯弧面温度低,处于700-900℃的第三脆性区,经过弯曲和矫直区域时,又恰好表面析出铝、铌等元素的碳氮化物致钢的延性下降,横裂纹得以形成。
4、主要影响因素剖析
4.1、保护渣结晶性能
各类裂纹对应的保护渣类别中,E保护渣产生裂纹量最多,小纵裂纹占39.96%。通过对2013年3季度250mm、300mm厚断面的生产数据统计(1976.074t小纵裂纹)保护渣性能与小纵裂纹关系可知。同一台连铸机浇铸中碳亚包晶钢轧制中厚板时,E-2渣按生产炉数统计,平均小纵裂纹非计划品量较多(4.823t/炉,裂纹率2.46%),D-2渣较少(0.374t/炉裂纹率0.19%),故亚包晶钢保护渣性能按D类渣设计,而同期浇铸含铜铝铌的低碳低合金钢的E-1渣小纵裂纹非计划品量处于二者之间(1.623t/炉,裂纹率0.83%),保护渣性能如表1所示。
表1:结晶器保护渣物理性能
|
E-1
|
E-2
|
D-2
|
R
|
1.28
|
1.62
|
1.78
|
Al2O3,%
|
4.48
|
5.83
|
2.28
|
粘度,Pa·S
|
0.113
|
0.063
|
0.038
|
转折温度,℃
|
1169
|
1167
|
1169
|
析晶比例(粗晶),%
|
20
|
20-30
|
100
|
半球点温度,℃
|
1098
|
1202
|
1083
|
4.2、班组操作差异
各班组操作对微裂纹的影响如表2所示。从表可见,丁班小纵裂纹较多,乙班较少;乙班边部横裂纹较多;甲班和乙班横裂纹较多,丁班较少;甲班边部纵裂纹较多。
表2:各班组裂纹非计划品分布
|
各班组在各类裂纹非计划品中
所占比例,%
|
出现裂纹炉次各炉平
均非计划品重量,t/炉
|
||||||
班别
|
甲
|
乙
|
丙
|
丁
|
甲
|
乙
|
丙
|
丁
|
边部纵裂纹
|
36.63
|
22.32
|
28.17
|
12.87
|
5.729
|
4.747
|
4.832
|
4.888
|
横裂纹
|
35.83
|
40.46
|
12.73
|
10.99
|
22.181
|
21.037
|
10.341
|
9.521
|
边部横裂纹
|
19.71
|
31.56
|
25.39
|
23.34
|
5.667
|
7.787
|
5.971
|
6.309
|
小纵裂纹
|
20.81
|
18.18
|
28.71
|
32.30
|
18.934
|
13.846
|
19.921
|
25.147
|
3号机同系列钢种小纵裂纹与班别的差异如表3所示。从表可见,丁班小纵裂纹较多(无论是稳态和非稳态),乙班较少。通过深入分析某段时间生产的上千吨的50mm厚钢板表面小纵裂纹非计划品的原因发现,供钢节奏、钢水成份保证和生产时铸机状态及连铸浇钢操作对小纵裂纹的形成也有较大影响。
表3:3季度班组小纵裂纹分布情况
|
甲
|
乙
|
丙
|
丁
|
合计
|
稳态产生小纵裂纹所占比例,%
|
17.88
|
2.12
|
3.18
|
25.04
|
48.22
|
非稳态产生小纵裂纹所占比例,%
|
4.13
|
4.35
|
14.62
|
28.67
|
51.78
|
生产炉小纵裂纹发生率,t/炉
|
2.033
|
0.549
|
0.983
|
3.674
|
1.820
|
4.3、连铸设备精度
对某些浇次生产板坯精整抽查板坯角部附近皮下裂纹时,发现多数板坯角部附近皮下存在边部纵裂纹,倒查结晶器状况,发现其窄铜板倒锥度在使用过程中已经出现从1.23%/m变为了1.00%/m,下降了0.23%/m。
从使用后的弯曲段夹辊磨损痕迹变化发现,离结晶器越远,板坯外弧角部与夹辊接触越明显,抽查板坯外弧质量时常发现角部横裂纹,说明结晶器足辊与弯曲对弧及弯曲垂直度均存在问题。
5、措施与效果
8月下旬开始强制推行保护渣事前检测的制度,供轧制厚板的板坯生产时所用结晶器保护渣,必须进行事前检测结晶率等理化性能,确保保护渣碱度、转折温度和结晶率在标准允许范围内,合格后方能使用,自此以后,小纵裂纹得到较好控制。
为解决200mm厚板坯的角部横裂纹,从6月开始修正对弧方法,8月完成,9月后完全按照新的要求落实了结晶器与弯曲段对弧和垂直度的正确检测方法,边部横裂纹明显降低。
解决含铜、铝、铌钢厚板的表面微裂纹,从7月开始狠抓供钢节奏控制,提高恒速浇铸率,减少化学成份超标率,优化二次冷却强度,确保操作到位,9月后基本实现该类钢种的微裂纹控制。
2013年10月至2014年2月供4100轧机的钢板微裂纹非计划品率0.36%,与2013年1月至9月的0.90%比较,下降幅度达60.00%。
6、结语
通过采用1.70以上碱度保护渣,同时强化保护渣性能事前检测、供钢节奏和化学成份控制,优化低拉速下二冷强度,对结晶器与弯曲段的对弧方法修正,设备精度得到有效保证,重钢钢板表面微裂纹得到有效控制,取得了明显的经济和社会效益。
收稿时间:2014年9月
来源:重钢