重钢炼钢新流程的创新设计和生产实践
2014-02-08 09:40:40
重庆钢铁集团(以下简称重钢)2009年其钢铁主业环保搬迁至长寿区,设计目标是建设21世纪新一代钢铁厂,做到产品洁净化和对环境的无害化,实现过程动态有序、连续紧凑和高效稳定。自主集成开发了“一罐制铁水运输→KR铁水脱硫→复吹转炉冶炼→干式真空等精炼→常规厚度高效板坯连铸→板坯热送热装”重钢炼钢新流程。一期工程产品定位于生产优质板卷钢和船用钢精品板材,设计产能650万t/a。该工程于2009年12月25日投产,2012年元月6日全部建成。在该项炼钢新流程运行过程中,对影响其顺行的各种问题进行了持续改进。
1、炼钢流程的再造
1.1、新流程的构成
重钢炼钢新流程如图1所示。
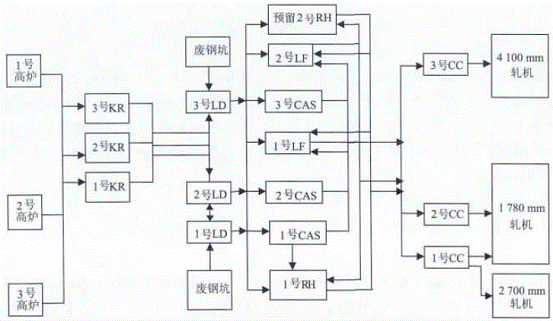
图1:重钢炼钢新流程示意图
1.2、界面技术
1.2.1、铁钢界面的“一罐制”
流程采用3座高炉与3座转炉(中心距360m)呈平行布置,高炉受铁罐与脱硫罐、转炉兑铁罐合一:用铁水罐车、行车代替标准轨铁路及机车完成铁水转运及高炉摆罐。脱硫站布置在铁水转运跨东侧1号、2号高炉出铁线之间,根据需要选择深脱硫、浅脱硫和扒渣。加料跨为“中间进铁、两端进废钢”的布置方式,同跨实现“双联”(脱磷、脱碳),既可传统冶炼又能双联冶炼。作为高炉与转炉间的缓冲,配有3200t/d的铸铁机,11个工位的铁水重罐支座,起到“虚拟混铁炉”的作用。
1.2.2、洁净钢平台和一钢多级生产模式
以建成高效低成本洁净钢生产平台和一钢多级品种钢生产模式为目标。采用KR铁水脱硫,带副枪顶底复吹转炉等核心技术确保以进入精炼环节的钢水质量;分钢种选择精炼单元对钢水进行处理,保证钢种对洁净度、温度和成分的要求;采用大容量中间包的直弧型连铸机促进钢中夹杂物的充分上浮。
以“一钢多级”为目标,简化炼钢生产品种分类。以多批钢板订货合同为一个单元,组长尺、组炉、组浇次,对组板设计产生的二次切割坯组合成一个炼钢切割长尺坯料;然后依据转炉单炉钢水平均重量,将一次切割坯组合成一个基本炉次;最后将组合好的炉次最终组成一个基本浇次,以每一个中间包浇次倒排炼钢生产计划。
1.2.3、钢轧界面热送热装
由辊道直接将板坯送至轧钢加热炉前(送坯距离约180~200m),1780mm轧机直接入炉,4100mm和2700mm轧机将板坯切割成轧制所需的长度入加热炉加热,堆坯和整钢共占一跨。供2700mm、4100mm中厚板轧机的代表钢种为高强船板钢,多数钢中含有铝、铌、钛,板坯容易出现表面纵裂纹、角部横裂纹等质量问题,因每个合同订货批量小,实现板坯热装难度大。供1780mm热轧板卷轧机的代表钢种为低碳钢、中碳钢、中低碳低合金钢等,板坯也容易出现表面纵裂纹、横裂纹等质量问题,易导致轧钢断料。
1.3、共性技术
1.3.1、KR脱硫
全量铁水KR脱硫保证供转炉炼钢的铁水温度、硫含量、顶渣量满足少渣炼钢要求,3套KR脱硫装置平均处理铁水198t、处理周期30min、处理后钢水w(S)=0.010%~0.002%。
1.3.2、转炉炼钢
带副枪210t顶底复吹转炉实现降碳提温和生产洁净钢的目标,平均出钢量210t,常规生产时冶炼周期38min,双联脱磷18min、双联脱碳30min,配有一、二、三次除尘系统,一次除尘回收煤气含尘量小于等于10mg/m3、吹炼期放散煤气时含尘量(脱碳时)小于等于15mg/m3。
1.3.3、二次精炼
精炼跨布置有干式真空(机械)泵RH和LF及CAS微调站,3种精炼方式的组合确保钢水质量。机械真空泵与蒸汽泵性能对比如表1所示。干式真空RH主要参数如表2所示。2座双钢水罐车、电极横臂旋转式、变压器额定容量36MVA的210tLF,平均升温速度4.5℃/min、平均处理周期30min。炼钢单元用低压蒸汽由炼钢余热锅炉蓄热站供给,85%以上蒸汽用于发电。
表1:RH干式(机械)真空泵和蒸汽泵的综合比较
泵型
|
工作能介
|
抽气能力配置
|
极限真空度/Pa
|
抽真空时间(67Pa)/min
|
脱氢能力/10-6
|
生产组织
|
除尘方式及效果
|
设备稳定性
|
能源成本
|
干式泵
|
电能
|
根据需要添加模块即可
|
18
|
4.34
|
0.9
|
根据要求随时启停
|
干法除尘,便于回收利用
|
性能稳定、维护量小
|
低
|
蒸汽泵
|
蒸汽
|
定型后无法变化
|
20
|
≤4.5
|
≤1.5
|
受蒸汽压力、温度影响;蒸汽泵预热时间≥30min
|
洗涤除尘、回收难度大
|
必须定期清理“喉口”,随使用时间延长抽气能力下降
|
高
|
注:脱氢能力为初始w(H)<4×10-6的脱氢能力
表2:重钢RH主要参数
型式
|
双钢包车、双真空处理位
|
钢水处理量
|
190~230t(平均210t)
|
67Pa时真空泵最大抽气能力
|
800kg/h
|
极限真空度
|
20Pa
|
平均精炼周期
|
20~30min
|
抽真空时间(66.7Pa)
|
≤4min
|
浸渍管
|
高度900mm,内径600mm,中心距1500mm
|
真空槽
|
内径2146mm,高度11558mm
|
浸渍管透气点
|
12个
|
驱动气体流量
|
90~180m3/h
|
1.3.4、板坯连铸机
3台连铸机均按高效化而设计,采用了钢包下渣自动检测技术、结晶器液位自动控制、大倒角结晶器(目前在3号铸机250和300mm厚断面使用)、结晶器液压非正弦振动、结晶器漏钢预报、动态轻压下和二冷动态配水、板坯表面质量在线检测等16项先进技术,其主要参数如表3所示。
表3:重钢板坯连铸机主要设计参数
铸机
|
断面
|
机型
|
流数
|
弧半径/m
|
结晶器长度/mm
|
拉速/(m·min-1)
|
冶金长度/m
|
钢种
|
1号
|
(160、190、230)mm×(1400~2000)mm
|
直弧型、连续弯曲、连续矫直
|
2
|
9.5
|
900
|
0.30~1.45
|
31.242
|
中、低碳钢、低合金钢、特殊低合金钢
|
2号
|
(190、230)mm×(850~1650)mm
|
直弧型、连续弯曲、连续矫直
|
2
|
9.5
|
900
|
0.30~1.60
|
33.901
|
超低碳钢、低碳钢、低合金钢、硅钢
|
3号
|
(200、250、300)mm×(2000~2500)mm
|
直弧型、连续弯曲、连续矫直
|
1
|
10.5
|
900
|
0.30~1.35
|
34.205
|
中、低碳钢、低合金钢、特殊低合金钢
|
1.3.5、信息系统
信息系统分一级基础控制、二级模型控制及数据信息采集、三级MES系统、四级ERP。
2、持续改进和实绩
2.1、铁水脱硫
“一罐制”运行不同阶段的转炉兑铁水温度稳定在1325℃,与2011年老区非“一罐制”的1270℃相比,温度提高了50℃以上。脱硫前平均铁水w(S)=0.029%~0.035%,石灰基脱硫剂深脱硫后铁水w(S)达到0.002%~0.005%,过程温降37℃,处理周期35.5min,脱硫率89.55%,脱硫命中率93.48%以上。工序技术经济指标如表4所示。
表4:重钢2010和2011年铁水脱硫技术经济指标
年份
|
铁水温度合格率(>1350℃)/%
|
KR脱硫罐数
|
单扒渣比例/%
|
脱硫率/%
|
KR脱硫命中率/%
|
脱硫粉剂消耗/(kg·t-1)
|
搅拌头寿命/次
|
2010
|
82.97
|
9242
|
15.08
|
84.92
|
85.01
|
7.15
|
180
|
2011
|
82.93
|
21277
|
10.45
|
89.55
|
93.48
|
7.23
|
130
|
2.2、转炉炼钢
废钢吸铁盘改为4m×1.7m,废钢斗头部改为圆形,缩短冷料准备时间;调整氧枪流量模式,减少转炉二次点吹次数,逐步提高转炉终点命中率;氧枪流量提高到48000m3/h,加快炉内化渣速度,缩短吹氧时间;提高出钢口质量和扩大内径,缩短出钢时间2.05min;在精炼跨和接受跨间增加过跨平车;改造精炼用行车副钩用于运转空钢包,降低行车转运压力;加强钢包维护和准备操作,提高钢包寿命,降低转炉等钢包比例至3.8%;转炉冶炼周期缩短7.05min,达37.95min,且转炉冶炼周期小于等于38min的比例达到92.32%。由于过程温度稳定,取消了正常炉次连铸平台测温操作。工序技术经济指标如表5所示。
表5:重钢转炉2010和2011年炼钢技术经济指标
年份
|
碳温双命中率/%
|
副枪成功使用率/%
|
氧耗/(m3·t-1)
|
石灰消耗/(kg·t-1)
|
转炉工序能耗/(kJ·t-1)
|
转炉蒸汽回收量/(kg·t-1)
|
转炉煤气回收量/(m3·t-1)
|
2010
|
67.58
|
95.26
|
58.95
|
47.43
|
-624510.86
|
94
|
78.25
|
2011
|
71.06
|
97.78
|
57.99
|
49.68
|
-525163.52
|
100
|
60.61
|
注:表中碳温双命中率的控制要求为:w(C)<0.06%时,误差为±0.01%;w(C)≥0.06%时,误差为±0.02%;温度误差±10℃
2.3、精炼工艺
根据钢种工艺路线制定不同的转炉脱氧模式和精炼工艺,通过优化顶渣脱氧工艺和RH碳脱氧工艺及对CAS和出钢过程吹氩管网改造,提高钢水洁净度,降低合金成本;低碳和超低碳钢系列以及部分低合金钢从“BOF→LF→CC”工艺路线分别转移为“BOF→CAS→CC“和“BOF→CAS→RH→CC”工艺路线,铝硅镇静钢和低碳低硅钢单中间包连浇炉数可分别达到19和17炉,基本杜绝了因钢包钢流跟不上致断浇的事故发生。RH出站经过26min的循环后钢水w(H)可控制到0.9×10-6以下,低碳低硅钢w(N)可控制在24.5×10-6以内,w(C)可控制在10×10-6,w(T.O)<25×10-6。精炼技术经济指标如表6所示。
表6:重钢2010和2011年精炼技术经济指标
年份
|
LF
精炼率/%
|
CAS
精炼率/%
|
RH
精炼率/%
|
RH出站钢水w(H)
≤2.0×10-6比例/%
|
2010
|
80.95
|
15.91
|
|
|
2011
|
41.38
|
44.55
|
27.62
|
96.73
|
2.4、连铸工艺
通过优化设备参数和操作,成功开发“宽板坯和双流板坯连铸机异钢种连浇中间包在线快换”技术。对3台连铸机的漏钢预报系统进行优化,结合人工方式以降低漏报率和提高预报准确率。结合生产实际拉速,优化中间包水口的设计,解决了水口流场均匀性不良的问题。对保护渣进行优化,板坯表面原始合格率达90%以上,粘结频率也在可控范围内。3台铸机动态轻压下、动态二冷水全部正常应用,铸机内部质量得到较大改善。对1、2号机1~8段二冷水进行“幅切”(结合使用偏喷嘴)控制的改造,板坯边角部横裂纹基本受控,2号机还满足了轧钢工序对230mm×(1030~1650)mm断面9个宽度快速更换的要求,生产的碳素钢热送比例达到90%以上。3号机通过采用偏喷嘴以适应次窄宽度板坯的二冷区温度控制的需要,2011年5月成功进行了碳素钢热送4100mm轧钢厂试验,10月进行低合金钢热送试验,试验炉次均达到轧钢要求。3号机(250、300)mm×2000mm断面上还进行大倒角结晶器试验,共生产钢265炉,57000t板坯,轧后与常规板坯经过角部倒角清理的裂纹率相当。连铸下渣检测、漏钢预报、轻压下、液位控制应用率均在95%以上。液位控制精度通常在±3mm内,超过±5mm报警。连铸技术经济指标如表7所示。
表7:重钢连铸机2010和2011年技术经济指标
年份
|
浇成率/%
|
恒速率/%
|
单中间包连浇炉数
|
铸机作业率/%
|
溢漏钢率/%
|
金属收得率/%
|
中间包温度合格率/%
|
2010
|
99.58
|
90.94
|
10.44
|
37.29
|
0.099
|
96.58
|
64.30
|
2011
|
99.89
|
93.02
|
12.76
|
62.63
|
0.020
|
97.62
|
92.82
|
2.5、洁净钢生产平台
重钢迄今为止实现了对老区钢种的替代,生产出的容器、锅炉、船板和桥梁用钢的性能比老区同类产品更好,按新的一钢多级牌号生产中厚板45个,热轧板卷17个钢种系列,其中新开发了15CrMoR、X60、热轧硅钢、取向硅钢、45、E40、E460、E47、Q550等钢种,钢水洁净度可达:w(S)≤10×10-6、w(P)≤20×10-6、w(O)≤15×10-6、w(N)≤20×10-6、w(H)≤1.4×10-6,洁净钢平台基本建成。2010年和2011年板坯质量指标如表8所示,全厂综合技术经济指标如表9所示。
表8:重钢2010和2011年板坯质量指标
年份
|
中厚板表面微裂纹率/%
|
板坯内裂率/%
|
低倍B类评级小于1.0级比例/%
|
探伤合格率/%
|
板坯表面原始合格率/%
|
板坯热送率/%
|
2010
|
0.74
|
0.029
|
72.97
|
99.36
|
71.85
|
|
2011
|
0.27
|
0.026
|
94.70
|
98.64
|
87.78
|
40.22
|
表9:重钢炼钢厂2010和2011年综合技术经济指标
年份
|
产量
/万t
|
平均炉
产量/t
|
钢坯综合
合格率/%
|
炼成率
/%
|
钢铁料消耗
/(kg·t-1)
|
综合能耗
/(kJ·t-1)
|
2010
|
186.976
|
206.15
|
98.69
|
95.52
|
1097.89
|
5275.08
|
2011
|
453.928
|
214.31
|
99.59
|
98.29
|
1083.40
|
-89090.24
|
3、结语
重钢炼钢新流程布置紧凑,厂内无蒸汽管网和铁路,物流时间短、占地少。全新的一罐制运输铁水、转炉一次干法除尘、干式真空RH、旋转臂LF、国产高效宽厚板坯连铸、板坯热送热装等新技术成功应用,生产秩序、品种开发、产品质量、技术经济指标等方面均取得显著进步。
收稿时间:2012年9月
来源:重钢