重钢冶金固体废弃物综合利用现状及发展思路
2012-06-14 08:38:25
循环经济是当今国际推进可持续发展的一种新型实践模式,它强调最有效利用资源和保护环境,表现为“资源-产品-再生资源”的经济增长方式,做到“污染排放最小化,废物资源化和无害化”,以最小成本获得最大经济效益和环境效益。循环经济的本质是生态经济,核心是资源的综合利用,资源综合利用是循环经济中的关键环节,是建立循环经济、落实可持续发展战略的有效途径。2009年1月1日,《循环经济促进法》颁布实施,如何综合利用冶金固体废弃物已成为各钢铁企业的当务之急。
重钢作为具有百年历史的钢铁企业,十分重视环境保护和资源综合利用,环保搬迁工程的实施使很多新的固体废弃物处理工艺、综合利用技术及机械设备得以应用,对减少废弃物排放,争取做到“零排放”,起到了积极地推动作用。在集团实现环保搬迁后,冶金固体废弃物综合处置利用率达到98%以上,目前正向全量利用的目标迈进。
1、重钢冶金固体废弃物综合利用现状
1.1焦化
在焦化工序产生的固废主要是:除尘灰(富含碳)、焦油渣(包括沥青渣和再生器残渣)和污泥(富含碳)等。该部分固废资源型煤化后全部返回焦化配煤进入炼焦工序,其工艺流程如图1、图2所示。
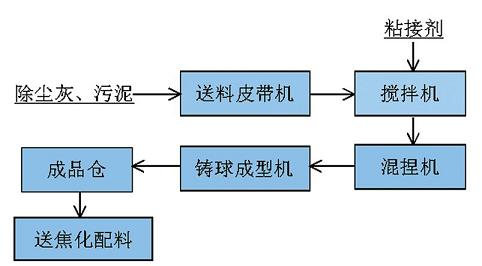
图1 除尘灰、污泥型煤生产工艺流程图
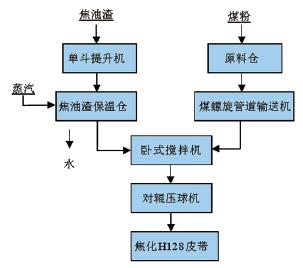
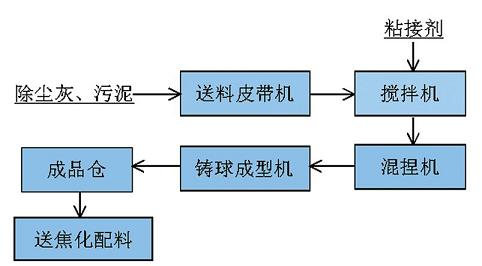
图1 除尘灰、污泥型煤生产工艺流程图
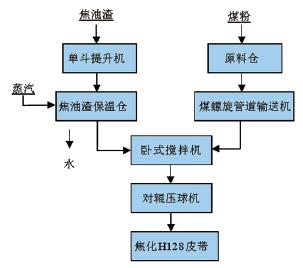
图2 焦油渣型煤生产工艺流程
1.2炼铁
炼铁工序所产生的固体渣资源主要是:高炉渣(俗称水渣)、除尘灰(出铁场除尘灰、槽下除尘灰、高炉炉顶除尘灰即瓦斯灰,瓦斯灰又分为粗瓦斯灰和细瓦斯灰,细瓦斯灰富含锌和铅)和废旧耐材。
重钢采用嘉恒法处理热态高炉渣,高炉水渣年产量约240万t。目前高炉渣供不应求,主要是销售给建材企业生产矿渣水泥和矿渣微粉。为了降低运输成本,在重钢厂区附近当地政府规划专属循环经济区,有关建材企业入驻并专门建有与重钢配套的大型粉磨站。
1.3炼钢(含连铸)
在炼钢工序产生的固废主要是:钢渣、废旧耐材、废钢(坯头、坯尾、废坯、中包余水等)、除尘灰、氧化铁屑、废油、污泥等。
当钢产量650万t/a时,钢渣产生总量约112万t/年。其中常规转炉渣约88万t/a、脱硫渣约14.1万t/a、铸余渣约8.8万t/a、中间包渣约0.7万t/a。
钢渣处理工艺为热泼、热闷两种处理工艺。根据渣源的物理与化学性质之间的差异,热泼工艺专门处理脱硫渣、铸余渣、散渣,必要时也可处理常规转炉渣;热闷只处理常规转炉渣。
热泼处理工艺:
卸罐挂钩→翻渣→渣罐喷涂→打水降温→渣铁分离→抓渣上料仓→进入破碎-磁选-筛分加工流程。
热闷处理工艺:
卸罐挂钩→翻渣→渣罐喷涂→行车抓渣入炉→打水闷渣→出炉→抓渣上料仓→进入破碎-磁选-筛分加工流程。
通过热泼、热闷处理后的钢渣经破碎-磁选-筛分加工后,含铁资源中60-200mm部分产品(重钢内部定义为炼钢用钢渣)返回炼钢厂直接入炉、含铁资源中-8mm部分产品(重钢内部定义为烧结用钢渣,俗称吸粉)返回烧结做烧结含铁原料、含铁资源中8-60mm部分产品(重钢内部定义为炼铁用钢渣,俗称吸子)再经水洗-球磨-磁选深加工(水洗-球磨-磁选深加工工艺)后其8-60mm部分产品返回炼铁厂做高炉原料。
钢渣尾渣,供周边建材企业做原料,例如:一部分供给重庆市富环建筑材料有限责任公司用来生产发泡混凝土及其制品,一部分供给重庆润江环保建材有限公司用来生产钢渣微粉,一部分用来生产水泥稳定钢渣道路基层材料等。
1.4轧钢
轧钢工序所产生的固体渣资源主要是:废钢(切头、切尾、钢板边、废次材)、氧化铁屑、废旧耐材、污泥(富含铁)、废油等。
重钢集团产业公司投资约9000万元建有与年综合产钢650万t配套的自产生产性废钢加工生产线,年加工废钢50万t(含重钢自产非生产性废钢),加工工艺流程如图3所示。
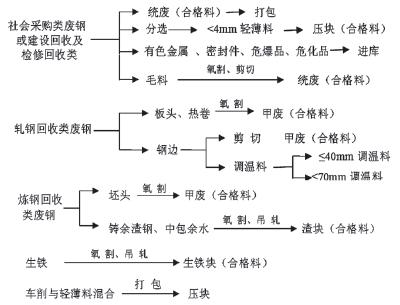
图3 自产生产性废钢加工工艺流程图
1.5氧化铁屑
重钢自产氧化铁屑来源于两方面,一是钢坯在加热过程中钢坯表面被氧化形成的氧化铁屑,另一部分是连铸和轧钢工序对连铸坯和钢材(含板材和型材)进行整定(例如:对连铸坯和钢材进行氧割等)时产生的金属熔滴物及其氧化物的混合物,俗称粗化渣。对氧化铁屑,采取人工筛分的方式,去除氧化铁屑中+8mm粒级的杂物,然后供烧结使用;对粗化渣,目前暂存。
目前,重钢集团产业公司正在建设与年综合产钢650万t配套的氧化铁屑加工生产线,该生产线的主要功能是:
第一、实现对氧化铁屑的筛分,筛出氧化铁屑中+8mm粒级的杂物后供烧结使用;
第二、实现对粗化渣进行破碎、筛分,-8mm粒级供烧结使用,+8mm粒级物料供炼钢或高炉使用。
该生产线总投资约300万元,将于2012年6月投产。
1.6除尘灰
含铁的除尘灰主要来源于料场、烧结、球团、炼铁和炼钢(含连铸),除炼铁的细瓦斯灰外的所有含铁的除尘灰目前处置工艺路径为:除尘灰+粘结剂——造球或制粒——配入烧结配合料;细瓦斯灰中富含锌和铅,简单返回烧结利用会造成高炉中锌和铅的富集,最终危及高炉的安全生产。目前,该部分细瓦斯灰全部堆存于料场待处置。
现在,重钢正积极进行调研,拟投资2-3亿元建年产15-20万t的转底炉,专门处理除焦化区域外的所有除尘灰,不但回收利用该部分除尘灰中含铁资源,还回收利用该部分除尘灰,特别是细瓦斯灰中的锌和铅,彻底消除由于回收利用除尘灰中含铁资源对高炉安全生产带来的不安全因素。
1.7废旧耐火材料
废旧耐材主要产生于炼钢(含连铸)和轧钢工序,在焦化、烧结(含球团)、高炉大修、中修时也要集中产生。
目前,重钢对废旧耐材的回收利用还停留在起步阶段,即在拆炉对耐材进行分选,然后将有用耐材投入再生产。废旧耐材回收主要用于生产再生镁碳砖(以转炉和钢包渣线用后镁碳砖为原料,经过拣选、除去表面杂质、水化等处理后进行镁碳砖再生)、再生镁铬砖(将用后镁铬砖按一定比例加入到RH的喷补料里)、钢包内衬废镁铝尖晶石浇注料重新利用(将回收的钢包内衬废镁铝尖晶石浇注料,以一定比例加水玻璃结合镁铝尖晶石浇注料中,取代原浇注料中的部分新料,不影响原浇注料的使用性能)、铝碳化硅质铁沟料等(利用废弃铁沟料生产的铝碳化硅碳质再生料,用于铝碳化硅碳转的生产)。
目前,重钢公司正对废旧耐材处理及综合利用进行调研,拟投资约1000万元建废旧耐材处理及综合利用生产线,该生产线的主要功用:
第一、在拆炉处对废旧耐材进行分选,将有用耐材投入再生产;
第二、分选剩余物进行“破碎-筛分-磁选”,充分回收废旧耐材中夹带、粘附的磁性金属物,然后将回收的金属物按粒级和含铁品位分送烧结和炼钢用。
该生产线拟于2013年建成投入使用。
废旧耐火材料再利用的工艺流程如下:拆炉→废弃耐火材料→分拣→分类→堆放→除去渣层→破碎磁选→处理→筛选→再生料规格品(按比例掺入到新品种中)→配料→混炼→困料成型热处理→制品。
在废旧耐材回收利用过程中,重钢只负责将废旧耐材拣选后加工成再生规格料,然后出售给重庆周边的耐火材料生产企业。
1.8其他固体废弃物
由于受目前资源综合利用技术的限制,并非所有的冶金固体废弃物都可以在现阶段实现资源化利用。比如:部分暂时不能利用废旧耐材、连铸除尘灰、石灰石焙烧单元水处理污泥、工业杂渣、中央水处理生产水处理污泥、生活污水处理污泥等,尽管以现有的技术无法循环利用,但为了使环境污染最小化、资源综合利用效益最大化,重钢专门规划了“重钢厂区外渣场”用以堆放或填埋此类固体废弃物,待技术进步后再加以处理综合利用。
2、重钢冶金固体废弃物综合利用的发展思路
总的说来,重钢冶金固体废弃物资源化综合利用以固废“全利用、零排放”为目标,近年取得了长足进步。目前,重钢基本完成了冶金固废中含铁资源的全量处理和回收利用,利用路径为:固废资源回收→烧结→高炉→炼钢→轧钢,即所谓大循环利用模式,但其利用仍处于低层次、低效率、低附加值、低梯级利用,表现为经济效益和环保效益的非最优化,如氧化铁皮、转炉泥及瓦斯泥的利用等,故在固废深度开发和高价值利用方面还有待进一步研究与发展。
重钢冶金固体废弃物资源化综合利用发展方向:
第一、在不产生二次污染的前提下,将废弃物资源作为相关行业的产品原料进行处理,保证了股份公司主体生产的正常,减少和消除废弃物的大量堆存,保证了生产主体的环保达标;
第二、建成各类综合利用项目,逐步形成综合利用产业、综合利用技术和产品体系;
第三,在对废弃物和副产品进行深加工的基础上,储备了部分技术含量高的项目(比如:转底炉项目、脱硫渣处理项目、铁粉还原项目等)。
通过这些综合利用确保清洁化生产,有利于减少污染,促进资源综合利用率的提高。同时,也给重钢本身带来新的经济增长点。
来源:重钢